Call us: +1-855-202-3299
Email: [email protected]
How to Leverage FMEAs and Control Plans for Continuous Improvement
Speaker: William A. Levinson
Speaker Designation: Principal Consultant, Levinson Productivity Systems
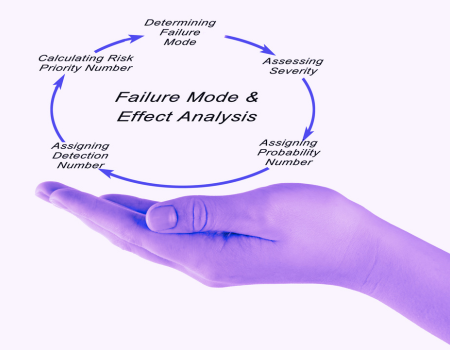
Call us: +1-855-202-3299
Email: [email protected]
Speaker: William A. Levinson
Speaker Designation: Principal Consultant, Levinson Productivity Systems
Process failure mode effects analysis (PFMEA) is part of advanced quality planning (AQP) or advanced product quality planning (APQP), whose purpose is to plan quality into the product realization process. It seeks to anticipate trouble in advance, in the form of failure modes, failure causes (also known as failure mechanisms), and failure effects. It then seeks to implement controls that prevent the generation of nonconforming products, or at least detect and stop them before they can reach an internal or external customer. It is required by the IATF 16949:2016 standard for automotive quality management systems (clause 8.3.5.2 (g)) and is highly recommended for ISO 9001 users.
This is a 90-minute overview of AIAG/VDA’s newest approach to process failure mode effects analysis, with additional information on (1) the role of FMEA in advanced quality planning (AQP), and (2) the control plan that can be appended to a PFMEA to create a dynamic control plan.
(Design FMEA will not be addressed, except for its role in AQP, due to time limitations and because some manufacturing organizations do not have a design in the scope of their quality management systems.)
Failure Modes and Effect Analysis can significantly impact your quality processes. It is critical to recognize that there are significant quality risks associated with failing to implement FMEAs when introducing new products or adapting existing ones.
The overarching goal of FMEAs and control plans is to proactively identify, mitigate, and address risks before they occur, which is beneficial to every company. Detecting failures before they significantly impact your manufacturing operations allows you to reduce potential threats, improve product reliability and quality, and increase customer satisfaction.
Mitigating, eliminating, or reducing these risks also means faster production time and, as a result, a shorter turnaround time to launch a new or updated product. Incorporating FMEAs into your operations can help you save money on quality. Forestall the quality problems before they occur to keep production flowing smoothly and ensure customer satisfaction.
William A. Levinson, P.E., is the principal of Levinson Productivity Systems, P.C. He is an ASQ Fellow, Certified Quality Engineer, Quality Auditor, Quality Manager, Reliability Engineer, and Six Sigma Black Belt. He is also the author of several books on quality, productivity, and management, of which the most recent is The Expanded and Annotated My Life and Work: Henry Ford's Universal Code for World-Class Success.