Call us: +1-855-202-3299
Email: [email protected]
5S or 7S Workplace Organization/Lean Manufacturing (What Happened to 6S?)
Speaker: Kenneth Zabel
Speaker Designation: Product Stewardship
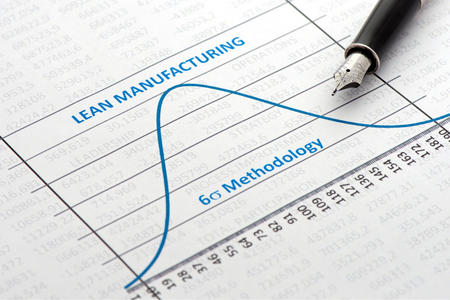
Call us: +1-855-202-3299
Email: [email protected]
Speaker: Kenneth Zabel
Speaker Designation: Product Stewardship
5S began as part of the Toyota Production System (TPS), the manufacturing method begun by leaders at the Toyota Motor Company in the early and mid-20th century. This system, often referred to as Lean Manufacturing in the West, aims to increase the value of products or services for customers. This is often accomplished by finding and eliminating waste from production processes. The term 5S comes from five Japanese words that each represent one part of a five-step process that can improve the overall function of a business:
In English these are often translated to:
Additionally:
5S and 7S are processes and methods for creating and maintaining an organized, clean, safe, and high-performance workplace. Having a disorganized workplace will cost you time, money, employee satisfaction, and likely create customer dissatisfaction. Implementing these processes is an easy and cost-efficient way of overcoming these barriers. The benefits to addressing these areas are many – including higher efficiencies, less stress, fewer accidents, higher levels of quality, fewer breakdowns.
In recent times, Safety has been added as the 6th S in the 6S model. The addition of this “new S” was fitting and a needed extension. This step involves ensuring that the operationalization of work and the work environment meet all required safety standards. However, 6S is often confused with 6 Sigma.
5S (and the 6th S - Safety) help to create a better working environment, reduce waste while improving efficiency, quality & safety. For the company, these tools turn into the bottom for all different Lean Manufacturing tools to be used. They are designed to help build a quality work environment, both physically & mentally.
7S - Spirit: As leaders understand the impact of company culture and the importance of respect for employees, the need for this additional component becomes clear. While some organizations successfully implement the traditional 5S (6th S) methods, many are choosing to add Spirit - 7S - as an additional piece to make explicit the reliance on the people factor and the need to continually keep it in mind as other steps are undertaken.